Uncovering the Potential: How Cobots are Revolutionizing Workplace Safety and Injury Prevention
- Devonics
- Feb 23
- 4 min read
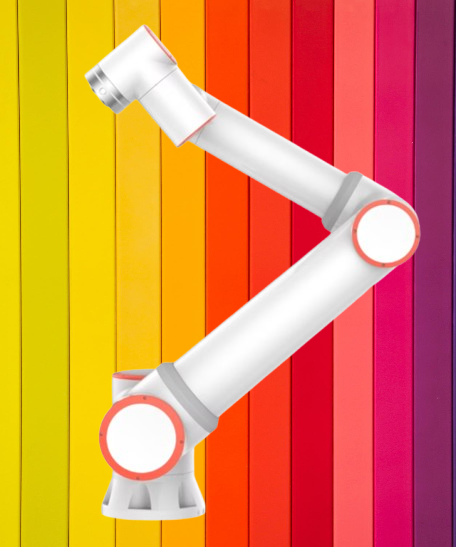
In recent years, collaborative robots, or cobots, have emerged as powerful tools in various industries. They promise not only to boost efficiency but also significantly improve workplace safety. Unlike traditional industrial robots that work independently, cobots are built to collaborate directly with human workers, often without the need for extensive safety barriers. This closer interaction offers a unique chance to transform workplace safety and minimize injuries.
In this blog post, we will examine how cobots enhance workplace safety, their role in injury prevention, and the impact of their use.
The Role of Cobots in Enhancing Safety
Cobots are essential in making workplaces safer by taking on hazardous tasks and reducing human exposure to dangerous conditions. They come equipped with advanced sensors and safety features, allowing them to detect nearby humans and react appropriately.
For example, in an automotive assembly plant, cobots can handle heavy components that would otherwise risk worker safety. By managing these challenges, they enable employees to concentrate on tasks that require more critical thinking instead of focusing on physical labor. Studies have shown that using cobots for heavy lifting can reduce workplace injuries by up to 50%, as workers experience less strain and fatigue.
Additionally, ergonomic designs in many cobots ensure they operate at optimum heights, further lowering the chance of injuries linked to lifting or repetitive motions.
Reducing Repetitive Motion Injuries
Repetitive motion injuries are a leading cause of workplace discomfort and absenteeism. In fact, the Occupational Safety and Health Administration (OSHA) estimates that these injuries cost U.S. companies around $20 billion annually in workers' compensation claims.
Cobots are particularly effective in environments with high repetition rates. For instance, in packaging facilities where tasks such as sorting, packing, or palletizing are common, these robots can perform the same actions with high precision and consistency. This automation can lead to up to a 60% decrease in the physical load on human workers, resulting in fewer injuries and reduced healthcare costs.
Furthermore, by relieving employees of monotonous tasks, cobots allow them to engage in more meaningful and varied work, which can boost job satisfaction and overall morale.
Accidental Injuries Prevention
Manufacturing environments often involve heavy machinery that can pose serious risks to workers. Cobots address this by taking over dangerous tasks and facilitating safer human-robot interactions. For instance, cobots equipped with force-sensing technology will halt operations if they come into contact with a person, significantly cutting the risk of injury.
Implementing cobots can lead to a noticeable drop in workplace accidents. According to a recent report, businesses that integrated cobots saw a 40% reduction in accidents over two years. Additionally, cobots can be programmed to operate only within defined areas, ensuring that human workers and machines do not overlap unnecessarily.
This collaborative safety approach encourages a culture of safety within organizations, making workers feel more secure in their environment.
Training and Support for Workers
Another significant benefit of cobots is their potential to aid in training new employees. New hires often feel anxious about operating complex machinery or performing delicate tasks. Cobots can act as training partners, demonstrating safe practices in real time.
For instance, in a manufacturing company, cobots might show new workers how to handle hazardous materials safely. By allowing new employees to learn alongside a cobot, workers gain hands-on experience, which can lead to a smoother transition into their roles.
This supportive learning environment not only builds confidence but also instills lifelong safe work habits.
Enhancing Emergency Response
Accidents can happen in any workplace, and prompt response times are crucial. Cobots can be programmed with specific protocols to assist in emergencies. In the event of a chemical spill, for example, cobots can quickly maneuver to the affected area to contain the spill, minimizing risks until human responders are ready.
Moreover, cobots equipped with real-time monitoring capabilities can continuously assess the work environment, identifying potential hazards before they escalate. This proactive safety measure allows organizations to mitigate risks effectively, adding another layer of protection for workers.
The Future of Cobots in Safety Regulations
As cobots become more prevalent in various industries, industry regulations and standards are adapting. Companies are increasingly acknowledging the potential for cobots to improve safety and productivity.
Future regulatory changes might include updating guidelines about human-robot interactions, establishing best practices, and creating mandatory safety measures. Clear regulations will be essential to ensure cobots are used safely and effectively, maximizing their benefits while protecting all employees.
The Transformative Impact of Cobots
The introduction of cobots signals a significant shift in safety practices and injury prevention. These robots contribute tremendously by decreasing exposure to hazardous tasks, minimizing repetitive motion injuries, and enhancing emergency response.
As technology evolves, the ways cobots can enhance workplace safety will likely expand. By adopting collaborative robots, organizations take vital steps toward improved safety and a culture of injury prevention.
Overall, cobots are more than just a technological improvement; they are critical partners in the mission to protect workers and create safer workplaces. The future promises increased collaboration between humans and robots, paving the way for a more secure work environment for everyone involved.